CAFE (Corporate Average Fuel Economy) standards will save new 2016 car buyers $4,000 in gas over the lifetime of the vehicle, say government analysts. In 2011, the Obama administration and vehicle manufacturers (OEMs) agreed on a CAFE fleet mandate of 54.5 MPG by 2025, OEMs must innovate to achieve the ever-growing number of miles a car or truck can travel on one gallon of gas.
However, in addition to the improved fuel efficiency, consumers rightfully demand the same power and torque. These market needs have caused rapid development in the automotive industry. OEMs are combining technologies—variable valve timing, hydraulic actuation, low tension piston rings and gasoline direct injection—to achieve a goal of small-engine efficiency with big-engine power.
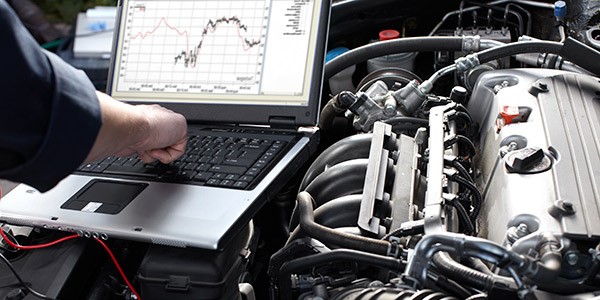
Variable Valve Timing (VVT)
In an effort to increase engine efficiency, automakers use Variable Valve Timing (VVT). In traditional 4-stroke engines, the intake and exhaust valves raise and lower at predetermined intervals. Driving conditions, or component operation variations, do not affect the rate at which the valves move.
Just as the name indicates, with VVT, the timing of the valve lift event (raising and lowering of the intake and exhaust valves) varies depending on RPM level, the piston’s current location and the valves’ current positions.
VVT is controlled by the cam phaser through hydraulic actuation. The cam phaser receives information from the Engine Control Unit (ECU), the engine’s computer.
The goal with VVT is to achieve optimum efficiency (at high and low RPM torque), increase fuel economy and reduce emissions.
VVT problems
As with many new technologies powered by hydraulic actuation, cam phaser functionality can be easily disrupted by fluid degradation. Engine oil integrity, oil filter flow-capacity and extended drain intervals can affect the ability of the cam phaser to control valve timing.
Hydraulic actuation is the process of converting power/pressure into mechanical motion using fluid. The lubrication system supplies power to turbochargers, timing chain tensioners and cam phase actuators, reducing the need for bulky, heavy mechanical parts. Hydraulic actuation improves fuel efficiency and reduces exhaust emissions by offering high power levels using lightweight actuation devices.
Because of the wide circulation of fluid with hydraulic actuation, fluid degradation can have a major affect on many different parts. Micro oil passages in the cylinder head, oil control valve and cam phasers can quickly become clogged with sludge. Sludge and varnish cause hydraulically actuated cam phasers to stick in advanced or retarded positions. When these intake and exhaust valves are open at the same time, hydrocarbon deposits can form on intake port walls.
All of this deposit buildup causes noticeable drivability and performance decline.
Low Tension Piston Rings
The purpose of piston rings is to build compression and prevent fuel and combustion gases from “blowing down” past the piston and oil vapors from seeping up into the cylinder.
Over time, piston ring changes were designed to allow less frictional drag energy loss, resulting in better fuel efficiency. Ideally, lowering tension pressure of the piston rings worked well to achieve “small engine efficiency,” but most manufacturers add turbochargers or superchargers to achieve the second part of their goal: “big engine power.”
Low Tension Piston Ring problems
Low tension piston rings buckle under extreme pressure and have a greater tendency to allow blow-by. Blow-by means that gasoline enters the crankcase resulting in oil degradation. Oil-based deposits are also being found in the combustion chamber. The result is deposits baked on piston tops and injector tips.
Add a turbocharger or supercharger to an engine with low tension piston rings and deposit buildup multiplies pandemically. These power boosters put a ton of extra pressure on the internal combustion process, which directly affects the job requirement of the piston rings.
When additives are depleted in the oil, it can no longer protect like it’s meant to. Deposits are a detriment to low tension piston rings. With such low spring force, the smallest amount of deposits quickly impedes ring movement. Stuck rings allow copious amounts of fuel and combustion gases to enter the crankcase, increasing crankcase temperature and pressure. This promotes excessive oil loss and deposit formation.
Gasoline Direct Injection
In Gasoline Direct Injection (GDI) engines, gasoline is sprayed directly where the combustion chamber is the hottest (instead of in the air intake) to allow for a more thorough, even burn. Ideally, a more complete combustion burn translates to better mileage and greater power.
GDI problems
In a port fuel injection engine, deposits can be “washed off” the backs of intake valves by a constant stream of gasoline in the intake. However, in a GDI engine the injectors spray inside the cylinders.
Without port injectors spraying gasoline (and the detergents that it contains) onto the backs of intake valves—intake components can quickly become caked with hydrocarbon deposits, restricting airflow.
GDI engines also run at much higher PCV and cylinder pressures, which in time, can allow oil vapors to pass by the piston rings. Oil vapors circulate into the cooler regions of the engine, creating deposits and pooling. Some of those areas include intake boots, valves, piston crown, head squish area and catalytic system.
A combination of sticky deposits and oil evaporation can lead to carbon buildup in several places in the engine. Rock hard carbon buildup fouls injectors and can dislodge and cause irreversible damage to cylinder walls and catalytic converters.
In just a few thousand miles, GDI engines have seen significant performance and MPG losses.
Solution
Rapid innovation—variable valve timing, hydraulic actuation, low tension piston rings and gasoline direct injection—answers the consumer call for, “We want it all!” But while exciting and solution-oriented, rapid innovation has its flaws.
At BG we know that with innovation comes opportunity. That, and it’s not always possible to have your cake and eat it too. Inherent problems, with each of these technologies, affect the oil and fuel systems.
The simple answer is that these problems can be avoided with three BG products. Thoroughly clean the piston rings (BG EPR® Engine Performance Restoration®). Fortify the oil to resist breakdown (BG Advanced Formula MOA®). Keep the fuel system deposit free (BG 44K® Platinum™).
These three products make the BG Performance Service BG’s most powerful maintenance service! The BG Performance Service will prevent deposit buildup and keep new technologies operating at maximum efficiency.
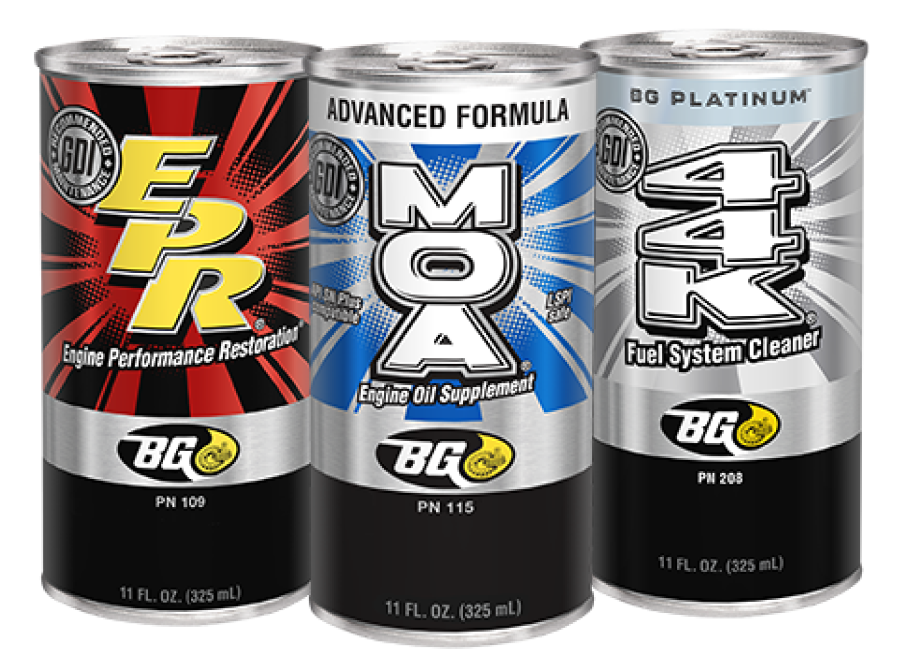