By Dustin Willhite, BG Director of Product Technology | Read time: 3 minutes |
As BG Products, Inc., continues to be the innovator and leader of automotive maintenance services, we proudly have expanded our corporate headquarters to house the brand new 34,000-square-foot BG Technology and Training Center.
The BG Product Technology Team is thrilled and incredibly grateful for their new space in the BG Technology and Training Center. This expansion will help further BG’s ability to push the envelope in automotive lubrication technology!
While great things were accomplished in the old building, it was definitely crowded. In fact, our former R&D building, including chemistry lab, offices, storage, a blending room and a secure place for flammables, was only a total of 3,600 square feet. The lab was sometimes bottlenecked and we didn’t have additional space for more staff to help keep up with our workload.
The new building has 2,550 square feet dedicated solely to testing. That’s not including the offices, blending room, storage room, and flammables storage. This upgrade has enabled BG chemists to increase the number of testing options and to add several new lab instruments to the space.
Best of all, we now have space to grow, and bring in new talented team members.
Saving time with new equipment
To reduce bottlenecks, we have doubled up on some testing instrumentation to increase throughput and get test results back, shortening project timelines. What’s more, we were able to add new equipment that cuts back on how much product we previously outsourced for testing.
By bringing much of this testing in-house, we have greatly reduced the proving time for new blends.
Safety first! Venting hoods and explosion-proof ovens
One of the significant improvements to the new chemistry lab is the addition of more venting hoods to capture fumes and odors generated by the testing process. The previous lab space had just two. Now we are breathing easy with seven venting hoods!
Any time a chemist is working with petrochemicals, the risk of fire is always a consideration. The new testing ovens house the heat source away from the oven cavity, making them explosion-proof.
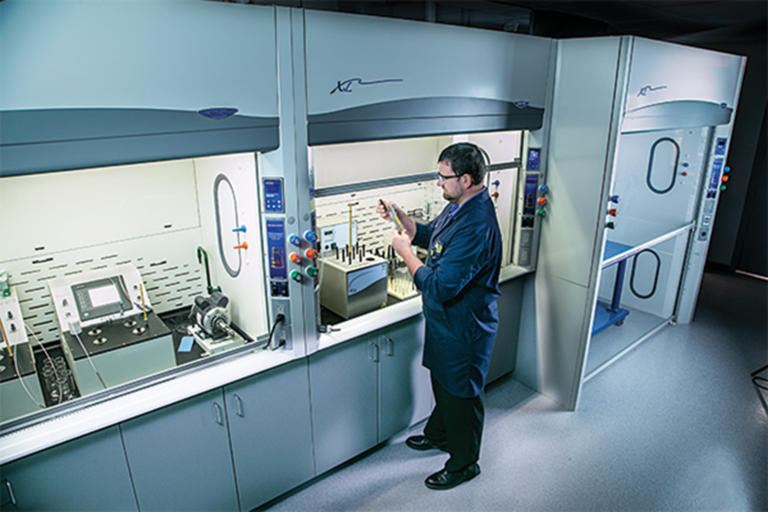
From lubricant stability to packaging safety
As engines become more efficient, they need lubrication that can tolerate higher pressure and more heat. New engine construction also features new metal alloys. The lubricant that does a good job of coating one metal may not work as well on another metal surface.
Testing for pressure tolerance, heat stability, and coating capacity can now be done in-house. KRL testing for shear stability of gear lubes and the four-ball test for extreme pressure enable BG professionals to study new products quickly and efficiently.
New engine oil testing capabilities allow products to be tested for high-temperature tolerance and to confirm shear tolerance. Previously, these tests were outsourced and receiving results back from outside testing could take weeks. Our team can now turn around these tests within days.
One of the tests performed in the new explosion-proof ovens is bottle compatibility. Our technicians check bottle compatibility by accelerating the aging process with heat. The bottles are filled, weighed and heated. Once cooled, they are weighed again to confirm that there’s been no escape of product during the heating process. Finally, the bottles are reviewed to make sure there is no change in shape or color.
Moving forward
Automotive technology is always expanding. As regulations push manufacturers to design smaller engines with more power, automotive lubricants will need to tolerate more heat and pressure. BG Products is always growing and is ready to meet these challenges. Thanks to new R&D facilities and great people, BG will continue developing products that will maintain advanced automotive systems.
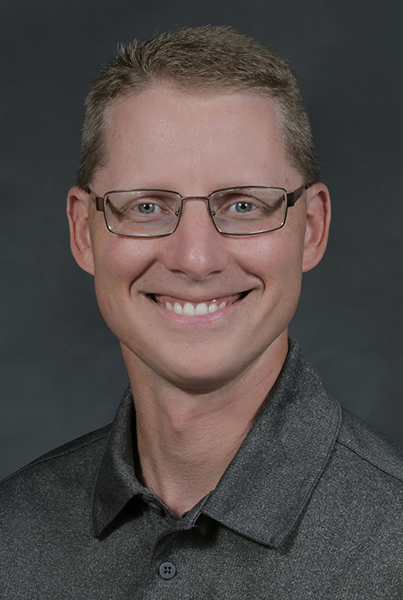
Dustin Willhite, BG Director of Product Technology
Dustin leads all product research and development, quality control and other technical services for BG Products, Inc.