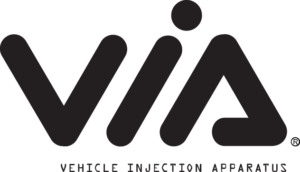
IMPORTANT! The following instructions must be read and understood before attempting to use the BG 12Q VIA®. Read product Safety Data Sheet before handling any BG product.
- Only a properly trained and certified technician may operate this apparatus.
- Make sure this service is performed in a well-ventilated area.
- Keep all hoses and tools away from moving engine parts.
- Check all lines, hoses, adaptors and points of connection for cracks and leaks before and after service.
- Do not spray solvents on flow indicator; clean using mild detergents only.
- Fluids being processed can approach 140°F/60°C and 90 PSI/6.21 Bar.
- Use extreme caution in handling hot hoses and adaptors.
- Use extreme caution opening vent and when installing and removing adaptors.
- Always bleed off pressure before and after each service or refill procedure.
The BG 12Q VIA® is designed to be used only with BG products described in these instructions. The use of any other chemicals or fluids with this system will void all warranties and could create hazardous conditions.
Initial Inspection
Before each use, inspect the general condition of the BG 12Q VIA®. Check for loose screws, misaligned or binding part of moving parts, cracked or broken parts, and any other condition that may affect the safe operation of the BG 12Q VIA®. If any of these conditions exist, have the problems corrected before further use. Do not use damaged equipment. CAUTION: All maintenance, service or repairs must be performed by a qualified service technician only.
- V2 process knob
- Flow indicator
- V1 pressure release
- G2 pressure gauge
- V4 vent valve
- V3 fill valve
- Service hose
- F funnel
- G1 engine vacuum gauge
- S heater switch
- Talk to the customer. Ensure the vehicle is a proper candidate for this service. It’s crucial that the customer communicates any and all drivability issues.
- Verify the complaint. Identify the root problem. It may not be what you expected. Look at set codes and proper EGR function.
- Perform visual inspection. If any component on the intake, the engine, or the exhaust system (e.g. EGR cooler) appears to have been tampered with, confer with the customer before proceeding.
- Apply the correct, necessary BG procedure. A BG Diesel Induction Service may need to be performed prior to a BG DPF & Emissions System Restoration Service. Make sure you have adequate training to perform the service properly.
- Perform the BG DPF & Emissions System Restoration Service as instructed. If you have followed steps 1–4, this service has a greater chance of success.
- Always test drive and clear all codes after the service.
- Install 32 oz. (946 mL) of BG 245 Premium Diesel Fuel System Cleaner, PN 24532, per 40 gallons of diesel fuel into the fuel tank.
- Hook up a recommended OEM or similar diagnostic scanner to the ALDL connector in the vehicle.
- Start the engine. Verify the scanner is communicating.
- Run engine to reach normal operating temperature (180°F/82°C).
- Attach appropriate spray nozzle to injector housing:
- For 7.0–8.0L engine, use 3.50 GPH spray nozzle and 14 hole injector housing
- For 8.0–9.0L engine, use 3.50 GPH spray nozzle and 16 hole injector housing
- For 9.0–10.0L engine, use 3.50 GPH spray nozzle and 18 hole injector housing
- For 10.0–11.0L engine, use 3.50 GPH spray nozzle and 20 hole injector housing
- Attach BG 12Q VIA® service hose to injector housing.
- Turn V3 Fill Valve to “Fill” (I) and V4 Vent Valve to “Open” (I).
- Fill the BG 12Q VIA® with BG DPF & Emissions System Restoration, PN 2581.
- For every 13 quart/liter volume crankcase capacity, use 1 gallon (3.7 L) of BG DPF & Emissions System Restoration.
- Turn V3 Fill Valve to “Close” (O) and V4 Vent Valve to “Close” (O).
- Apply shop air to the BG 12Q VIA® coupler. G2 Pressure Gauge should read 90 PSI.
- Plug in to power source.
- Turn vehicle engine off.
BG DPF & Emissions System Restoration Service
PROCEDURE
- Separate air tube located at the engine air intake manifold.
- Install BG Universal Diesel Intake Adaptor to the air intake, make sure there is a solid seal, then install BG Injector Atomizer into the BG Universal Diesel Intake Adaptor.
- Air tube
- To air intake manifold
- BG Universal Diesel Intake Adaptor
- BG spray nozzle & injector housing
- BG 12Q VIA® service hoses
- BG Injector Atomizer
- Start engine and, at idle, confirm:
- Engine is at operating temperature (180°F/82°C).
- G1 Engine Vacuum Gauge reflects 1” Hg/100 RPM. Note: 10” Hg at 1,000 RPM is the minimum.
- Scanner data stream is communicating and monitoring each system.
- Scanner is set to read vehicle RPM, EGR temperature sensor and all Exhaust Gas Temperatures (EGTs).
- Identify sensor position pre- and post-DOC, DPF and SCR.
- Disconnect MAF sensor if equipped. If not, disconnect the EGR and throttle motor.
- Accelerate engine to 1,200 RPM, check G1 Engine Vacuum Gauge reading and allow the EGT sensor (pre-DPF) to reach approximately 500–550°F/232–287°C and stabilize.
Note: In general, the DPF inlet temperature should exceed the DOC temperature within approximately 15 minutes from the setting of the RPM level in a properly functioning system. If this is not observed, there is a reason. Common reasons include the DOC being coated with engine oil or coolant. The DOC may need time to bake off contaminants. Leave the RPM level set at 1,200 RPMs and monitor temperatures. It may take as long as one hour for the DOC to bake. Success is observed by two things: (1) a large billow of white smoke coming out of the exhaust stack and (2) the DPF inlet temperature climbing as expected.
- Turn Heater Switch (S) to “On” (I) and wait 5 minutes for BG 12Q VIA® to reach operating temperature.
- With all the engine parameters stable, turn V2 knob to “Process” (I). Make sure the flow indicator shows fluid flowing.
- Closely monitor the scanner data for any sign of rapid increase in Exhaust Gas Temperatures. RPM/vacuum may need to be adjusted to maintain DPF temperature of 900–1,150°F/510–620°C.
WARNING: Reaching the maximum temperature differential could activate the vehicle’s protection parameters and shut down the engine. If maximum temperature differential is reached, turn V2 knob to “Close” (O) immediately. If for any other reason the engine shuts down, turn V2 knob to “Close” (O) immediately.Note: Raising RPM will increase temperatures and vacuum; lowering RPM will decrease temperatures and vacuum. Adjust in 100 RPM increments. If any of the EGT sensors reach 1,200°F/650°C or rapid increase in temperature is observed, turn V2 knob to “Close” (O), allowing the temperature to decrease and stabilize. Turn V2 knob to “Process” (I) to complete service.
- After flow indicator is clear, turn V2 knob to “Close” (O).
- Turn Heater Switch (S) to “Off” (O). Remove shop air. Press and hold the V1 Pressure Release until G2 Pressure Gauge reads “0.”
- Return vehicle to idle and run for at least 15 minutes.
- Monitor scanner data to make sure engine and cooling cycle of the DPF system are functioning properly.
- After exhaust systems have cooled, turn engine off.
- Remove adaptors.
- Reconnect air tube and EGR.
- Perform BG Diesel Engine Performance Service installing 32 oz. (946 mL) of BG EPR,® PN 109, and 32 oz. (946 mL) of BG DOC,® PN 112, per 10–16 quarts/liters of diesel engine oil.
- Test drive vehicle and clear any codes set during the service.
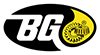